Description
Industrial soundproofing, or noise control in Nairobi, Kenya, is primarily governed by the Environmental Management and Coordination Act (EMCA) of 1999 and the Noise and Excessive Vibration Pollution (Control) Regulations of 2009. These regulations set permissible noise levels for various zones, including industrial areas, and emphasize the responsibility of industries to mitigate noise pollution. The National Environment Management Authority (NEMA) plays a crucial role in enforcing these regulations. And county governments, such as Nairobi City County, also have a significant part in local enforcement. Key aspects include the requirement for industries to obtain licenses for noise emissions exceeding permissible limits and the establishment of standards for noise measurement and control. The regulations aim to protect public health and ensure environmental tranquility by limiting excessive noise from industrial activities. Compliance is essential to avoid penalties and contribute to a healthier urban environment.
Industrial soundproofing is a critical field that focuses on reducing noise levels in industrial settings involving heavy machinery and processes that generate significant noise, which can have detrimental effects on worker health.
The primary objectives of industrial soundproofing revolve around creating a safer and more productive work environment. This involves significantly reducing occupational exposure to harmful noise levels, thereby mitigating the risk of hearing damage and other health complications for workers. Furthermore, soundproofing aims to enhance overall workplace well-being by minimizing noise-induced stress and distractions, which can improve employee concentration and productivity. Compliance with regulatory standards, such as those set by OSHA, is also a crucial objective, ensuring that industrial facilities adhere to permissible noise limits. Additionally, industrial soundproofing seeks to minimize noise pollution that may impact surrounding communities, fostering positive relations between industrial operations and their neighbors. Ultimately, the goal is to implement effective noise control measures that contribute to a healthier, safer, and more harmonious industrial environment.
Sources of industrial noise and their parameters
There are several types of industrial noise: mechanical, aerodynamic, hydrodynamic, technological, thermal, and explosive. The causes of their occurrence are different.
In particular, noise sources may be stationary technological equipment or hand-held mechanized tools, compressor or pump units, transport, forging, smelting, and other equipment used in organizing technological processes.
Depending on their origin, different types of industrial noise have different characteristics, which include:
The set of characteristics of each specific noise determines how it is perceived by a person and how harmful the impact is.
Current industrial safety standards differentiate existing noise in workplaces according to several criteria:
- According to the strength of noise impact, into classes A, B, C and D.
- According to the spectrum characteristics – broadband and tonal.
- By pitch, high-frequency, and low-frequency.
- By time parameters – constant, pulsed, oscillating, or intermittent.
Different types of noise have different effects on the human body. For example, prolonged exposure to low-volume sounds can cause increased fatigue. And even a one-time short-term exposure to loud sounds can lead to damage to the hearing organs and other health problems.
Vibration that occurs when machines and mechanisms operate is no less harmful; some of these mechanical vibrations directly affect the body, while others are transformed into low-frequency sound waves, which can also cause health problems.
1. Engineering Controls in Industrial Soundproofing
Isolation and Enclosures in Industrial Noise Control
In the realm of industrial noise control, isolation and enclosures stand as vital strategies for mitigating excessive sound levels. Enclosing noisy equipment involves constructing barriers around the sound source, effectively containing the noise within a defined space. These enclosures are often custom-designed, taking into account the specific characteristics of the machinery and the required level of noise reduction. Materials used in these enclosures are chosen for their sound-absorbing and sound-blocking properties, and the designs include features like access doors, ventilation systems, and viewing windows, ensuring functionality without compromising noise control.
Complementing enclosures, isolating vibrating machinery with anti-vibration mounts addresses the transmission of vibrational noise. These mounts, often made of materials like rubber or specialized polymers, are placed between the vibrating equipment and the supporting structure. By decoupling the machinery from the surrounding environment, these mounts significantly reduce the transfer of vibrations, preventing them from propagating as sound waves through floors, walls, and other surfaces. This method is particularly effective for machinery that generates significant vibrations, such as heavy presses, compressors, and pumps.
The combination of enclosures and anti-vibration mounts offers a comprehensive approach to industrial noise control. Enclosures contain airborne noise, while anti-vibration mounts minimize structure-borne noise. This dual strategy is essential for creating a safer and more comfortable work environment, protecting workers from hearing damage and improving overall productivity. Furthermore, the correct utilization of these techniques helps the industry to comply with regulations regarding noise pollution.
Sound Absorption and Damping
When addressing industrial noise, it’s essential to consider how sound behaves within a space and how it’s generated by machinery. Therefore, applying sound-absorbing materials, using damping materials, and installing silencers are all valuable strategies.
Here’s a closer look:
Applying sound-absorbing materials to walls and ceilings
Sound-absorbing materials play a crucial role in industrial soundproofing by effectively converting sound energy into heat. This process occurs within porous materials like acoustic foam, fiberglass, or mineral wool, where the intricate network of fibers creates numerous air pockets. When sound waves penetrate these materials, they cause air molecules to move within these pockets. This movement generates friction between the air molecules and the material’s fibers, resulting in the dissipation of sound energy as heat.
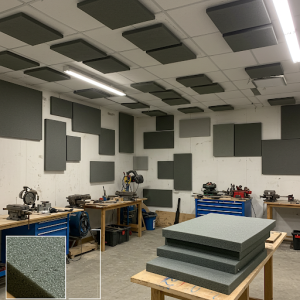
This mechanism is particularly effective in reducing reverberation, a common issue in industrial environments. Reverberation refers to the persistence of sound after its source has ceased, caused by sound waves reflecting off hard surfaces. By absorbing these reflected waves, sound-absorbing materials minimize reverberation, creating a more comfortable and less noisy environment. This reduction in reverberation improves speech intelligibility and reduces overall noise levels, contributing to a safer and more productive workspace.
The application of these sound-absorbing materials can be tailored to the specific needs of the industrial space. They can be installed as panels or tiles, offering a modular and visually appealing solution for walls and ceilings. Alternatively, spray-on applications provide a seamless and adaptable option for irregular surfaces or large areas. The choice of application method depends on factors such as the size and shape of the space, the desired aesthetic, and the required level of noise reduction. The correct application of these materials reduces the overall noise level and also improves the quality of the sound within the space, making it a more pleasant place to be.
Using damping materials to reduce vibrations in machine panels
Vibrating machine panels are a significant source of noise in industrial settings, with these vibrations propagating throughout the facility. Damping materials are applied to these panels to mitigate this issue. Viscoelastic compounds and constrained-layer damping systems are common examples. These materials function by converting vibrational energy into heat through internal friction.
When a machine panel vibrates, the damping material deforms. This deformation generates friction within the material, effectively dissipating the vibrational energy as heat. This process reduces the amplitude of the panel’s vibrations, leading to quieter operation. This technique is especially effective for large, flat surfaces, like those found on metal panels of presses, conveyors, and enclosures, which tend to resonate and amplify noise.
By reducing these vibrations, damping materials contribute to a quieter and more comfortable working environment. This not only protects workers from potential hearing damage but also enhances overall productivity by minimizing distractions.
Installing silencers on air exhausts
Industrial machinery like compressors, fans, and pneumatic tools often produces substantial noise from their air exhausts. Silencers are engineered to combat this, effectively reducing the noise generated by these airflows. These devices function by channeling the air through a series of chambers or baffles. This process absorbs or redirects sound waves, significantly diminishing the velocity and turbulence of the airflow, leading to quieter operation. Various silencer types exist, tailored to specific applications and noise reduction demands. By implementing these silencers, industries can successfully lessen noise pollution, fostering a safer and more productive work environment. This not only protects workers’ hearing but also improves overall workplace comfort.
Barriers and Screens for Industrial Soundproofing
Noise barriers and screens are essential tools in industrial soundproofing, functioning by strategically blocking the direct path of sound waves. Erecting these barriers involves constructing physical partitions, often made of dense materials like concrete, metal, or specialized acoustic panels, to intercept and deflect sound propagation. These barriers are particularly effective in outdoor or large indoor spaces where enclosing the entire noise source is impractical. Their height, length, and material composition are carefully chosen to match the specific noise reduction requirements.
Complementing physical barriers and optimizing the workspace layout play crucial roles.
Increasing the distance between noise sources and workers diminishes the intensity of sound reaching personnel significantly. This approach leverages the natural attenuation of sound over distance, reducing exposure levels. Strategic placement of machinery, workstations, and quiet zones within the facility can minimize noise exposure without requiring extensive structural modifications. This combination of physical barriers and optimized layouts provides a practical and effective method for controlling industrial noise, contributing to a safer and more comfortable work environment.
2. Administrative Controls in Industrial Soundproofing
Administrative controls in industrial soundproofing focus on managing worker exposure to noise rather than directly altering the noise source. Creating quiet zones is a key strategy within this approach. Establishing designated quiet areas for breaks and rest provides workers with respite from high noise levels, reducing their cumulative exposure. These zones are typically located away from noisy machinery and constructed with sound-absorbing materials to minimize ambient noise.
The effectiveness of quiet zones relies on their accessibility and enforcement. Workers must be encouraged to utilize these areas during breaks and rest periods. Scheduling breaks strategically can also help distribute noise exposure throughout the workday. Additionally, clear signage and physical barriers can delineate quiet zones, ensuring they remain free from excessive noise. By implementing and maintaining these quiet zones, industries can significantly reduce the risk of noise-induced hearing loss and improve worker well-being, complementing engineering controls and personal protective equipment. This approach demonstrates a proactive commitment to occupational health and safety.
3. Personal Protective Equipment (PPE) for Noise Control
In industrial noise control, earplugs and earmuffs serve as crucial personal protective equipment (PPE). Providing these devices is only the first step; ensuring their proper use is equally vital. This involves training workers on correct insertion techniques for earplugs and proper fitting for earmuffs, as well as emphasizing the importance of consistent wear in noisy environments.
Selecting appropriate PPE requires careful consideration of noise levels and frequency. Different earplugs and earmuffs offer varying levels of noise reduction, measured in decibels. Workers should be provided with PPE that adequately reduces noise exposure to safe levels, based on thorough noise assessments. Regular inspections and maintenance of PPE are also essential to ensure continued effectiveness.
Key Considerations in Industrial Soundproofing
Noise Measurement for Industrial Soundproofing
Accurate noise measurement is the cornerstone of effective industrial soundproofing. Conducting thorough noise assessments is crucial to pinpointing problem areas and quantifying the extent of noise exposure. These assessments involve utilizing specialized equipment, such as sound level meters and dosimeters, to measure sound pressure levels and personal noise exposure across the workspace. The process should encompass both stationary and mobile noise sources, as well as the ambient noise levels present.
The data gathered from these assessments provides essential insights into the frequency and intensity of noise, allowing for the identification of specific areas where noise control measures are most needed. By creating noise maps and analyzing the data, industries can prioritize interventions and select the most appropriate soundproofing strategies. Detailed noise assessments also enable the evaluation of existing control measures, ensuring their effectiveness and identifying areas for improvement. Furthermore, these assessments provide the necessary documentation for compliance with occupational noise exposure regulations, safeguarding worker health, and minimizing potential liabilities.
Adhere to Industrial Soundproofing Regulations
Adhering to industrial soundproofing regulations is paramount for ensuring worker safety and legal compliance. Occupational noise exposure limits, set by regulatory bodies, define permissible noise levels and exposure durations. Industries must conduct regular noise assessments and implement control measures to stay within these limits. This includes providing appropriate hearing protection, implementing engineering controls, and establishing administrative procedures. Failure to comply can result in penalties and legal repercussions, emphasizing the importance of staying informed and proactively addressing noise hazards.
Continuous Improvement of Industrial Soundproofing
Continuous improvement is key to effective industrial noise control. Regularly evaluating existing noise control measures ensures their ongoing efficacy. This involves periodic noise assessments, worker feedback, and reviews of maintenance records. Identifying weaknesses or areas for optimization allows for timely adjustments and upgrades. Embracing new technologies and best practices further enhances noise reduction efforts. This iterative approach promotes a proactive safety culture, minimizing noise exposure and safeguarding worker well-being.
By combining these strategies, industries can significantly reduce noise levels and protect their workers from hearing damage.